In-space manufacturing is a groundbreaking technology that is transforming how we approach space exploration and utilization. By producing necessary components and tools directly in space, we can significantly reduce the cost and complexity of space missions. This page focuses on the current in-space manufacturing technologies that are installed and operating in space, showcasing the advancements that are paving the way for future innovations.
1. Plastic 3D Printers:
- Additive Manufacturing Facility (AMF): The Additive Manufacturing Facility, developed by Made In Space, is the first commercial 3D printer permanently installed on the International Space Station (ISS). The AMF allows astronauts to print a variety of tools, components, and spare parts using plastic materials. This technology not only reduces the need to send spare parts from Earth but also enables rapid prototyping and iterative design improvements in real-time.
- Refabricator: The Refabricator, developed by Tethers Unlimited, is another innovative 3D printer on the ISS. It combines recycling and additive manufacturing in a single device. The Refabricator can process plastic waste generated on the ISS, such as packaging materials and used tools, and convert it into raw material for 3D printing new objects. This closed-loop recycling system enhances sustainability and resource efficiency in space.
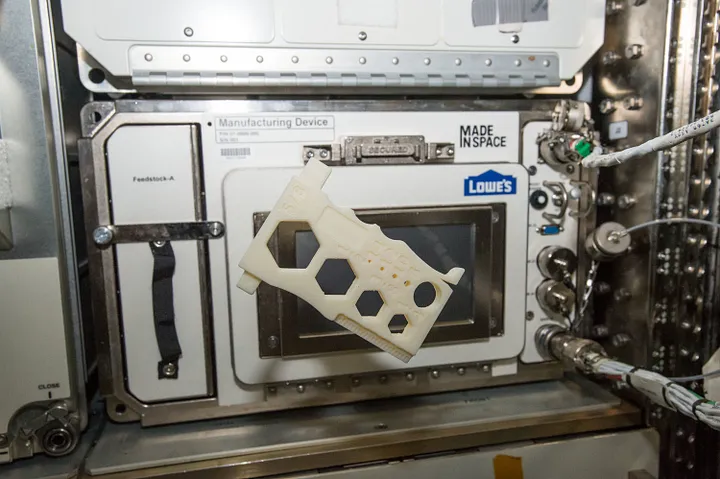
A printed product floats on ISS in front of the Adiditve Maufacturing Facility. (Image Credit: NASA)
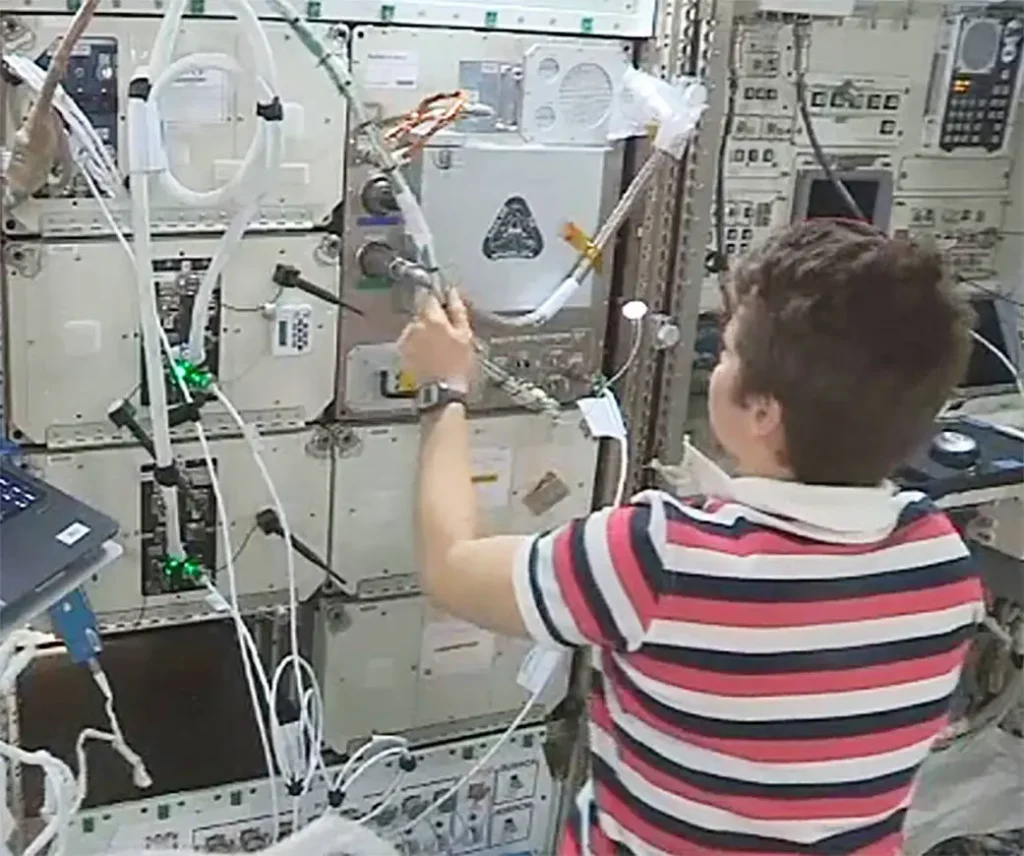
Refabricator was successfully installed onboard the International Space Station into the station’s experiment racks. (Credit: NASA)
2. Metal 3D Printer:
- First Metal 3D Printing on Space Station: The first metal 3D printing aboard the ISS marks a significant leap forward for in-orbit manufacturing. This milestone was achieved with a small s-curve deposited in liquefied stainless steel inside ESA’s Columbus laboratory module. The success of this initial test print, overseen by ESA technical officer Rob Postema and conducted by an industrial team led by Airbus Defence and Space SAS, paves the way for printing full parts in the near future.The Metal 3D Printer technology demonstrator, developed under contract to ESA’s Directorate of Human and Robotic Exploration, uses stainless-steel wire fed into a high-power laser-heated printing area. The wire melts in the heated zone to add metal to the print. Operations are managed from the ground, with minimal intervention required from the onboard crew. This technology aims to enable astronauts to produce necessary tools and components in space, significantly enhancing mission flexibility and reducing dependency on Earth-based supplies.
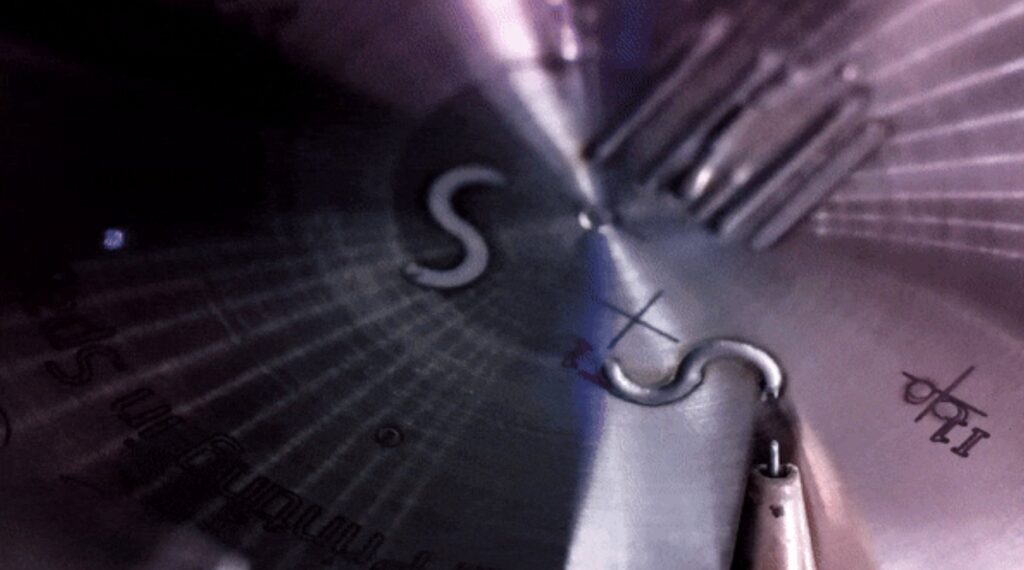
The first S-curve metal printed on ISS (Credit : ESA/Airbus)
3. Multi-Material 3D Printers:
- Redwire Regolith Print (RRP): Developed by Redwire (formerly Made In Space), the Redwire Regolith Print is an advanced 3D printer that can utilize multiple materials, including simulated lunar regolith (moon dust). This printer demonstrates the potential for using local materials found on the Moon or other celestial bodies to construct habitats and other structures, reducing the need to transport materials from Earth.
4. Fiber Optic Cable Manufacturing:
- FOMS Inc. has successfully demonstrated the production of high-quality ZBLAN fiber optic cables on the ISS. FOMS reported on November 7 that they completed the calibration of their manufacturing hardware and produced the first optical fiber in orbit. According to FOMS Principal Investigator Dmitry Starodubov, the microgravity-produced fiber showed better uniformity compared to Earth-based production, which can significantly enhance the performance and efficiency of optical fibers. FOMS’ Space Facility for Orbital Remote Manufacturing (SpaceFORM) was installed on the ISS with the support of astronauts and controlled remotely from the Marshall Space Flight Center. The fibers produced in space were returned to Earth for analysis, and NASA confirmed the high quality of these fibers. The microgravity environment allows for the production of fluoride-based optical fibers with fewer imperfections, potentially improving data transmission efficiency by up to 100 times compared to silica-based fibers. This advancement, supported by the ISS National Laboratory, represents a significant opportunity for both government and commercial sectors, potentially revolutionizing the global telecommunications system.
- Made In Space: ZBLAN is a type of fluoride glass used to produce high-quality fiber optic cables. Made In Space has developed a manufacturing process for producing ZBLAN fiber optic cables in microgravity, resulting in fewer imperfections and higher performance than those produced on Earth.
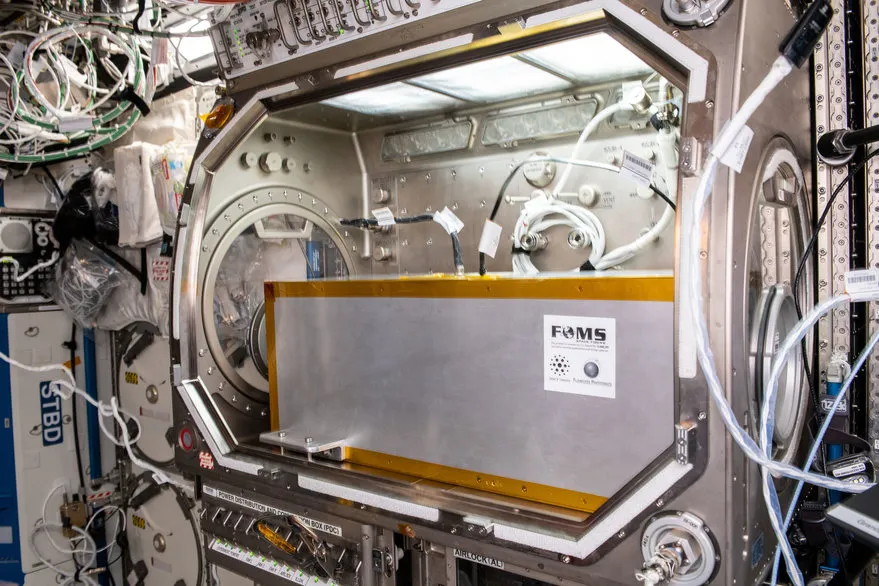
Fiber Optic Manufacturing in Space (FOMS). Credit: FOMS
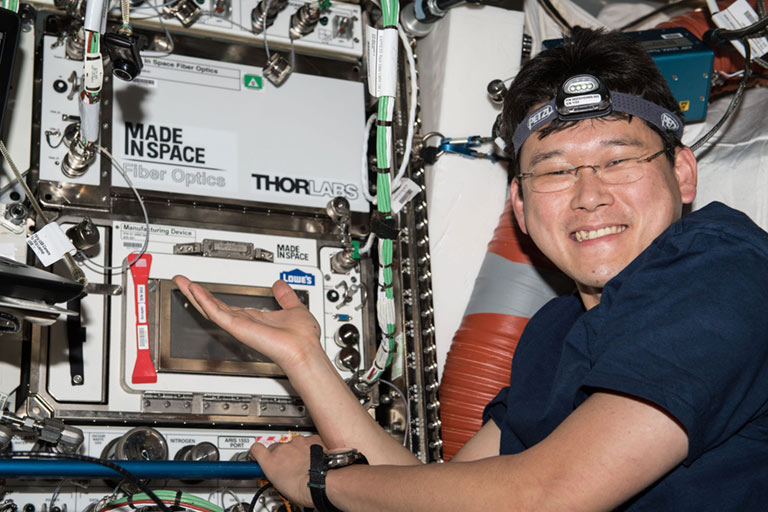
The MIS Optical Fiber Production in Microgravity (OFPIM) payload. Credit: NASA