What Are Fiducial Markers and When Are They Used?
Fiducial markers are essential tools used in space missions to help spacecraft accurately align during operations like rendezvous, docking, and servicing. These simple yet effective visual aids enhance navigation systems, ensuring precise positioning when two spacecraft need to interact. They are particularly valuable for missions involving older satellites not originally designed for servicing.
By integrating fiducial markers early in the spacecraft design, companies can prepare for future servicing operations such as repairs or refueling. These markers improve efficiency and accuracy, making them a key element in modern space technology.
Fiducial markers are critical for enhancing the technical accuracy of spacecraft during in-orbit servicing operations. They provide precise visual reference points, allowing servicer spacecraft to determine the position, orientation, and distance to the client object. This data improves relative navigation systems, enabling safe and efficient maneuvers.
When incorporating fiducial markers, companies must consider factors like optimal placement, the number of markers required, and compatibility with servicing technologies. Following established international standards ensures interoperability across various missions and agencies, making fiducial markers a versatile solution for enhancing spacecraft serviceability.
Fiducial markers follow specific standards depending on the space agency and region. NASA, JAXA, and CNSA each have their own guidelines for fiducial marker design, placement, and usage. These standards ensure that markers are compatible with autonomous navigation systems and other spacecraft servicing technologies.
For companies, it is essential to comply with the standards relevant to their mission’s operational region. Following these protocols guarantees smoother collaboration and ensures that fiducial markers function correctly during international or multi-agency space missions.
The Need for Adaptable In-Space Manufacturing
Additive manufacturing has transformative potential for space missions, allowing essential parts to be printed directly on-site. However, previous experiments with 3D printing in space have shown that simply uploading a CAD file and pressing “print” is not sufficient in a microgravity environment. Printing successfully in space requires precise adjustments to account for the unique conditions of zero gravity, temperature shifts, and limited material availability. Our mission is to adapt commercial 3D printing software to meet these space-specific needs, ensuring reliability and resource efficiency with every print.
Our approach to making commercial 3D printing software space-ready involves both technical enhancements and robust support tools. At TRL2, our solution includes:
1. Space-Ready API Integration – By embedding redundancy and adaptability, our API ensures that the software can function reliably in space.
2. Best Practices and Documentation – We provide comprehensive documentation that outlines best practices for in-space additive manufacturing, backed by checklists and adjustment protocols tailored to space conditions.
These tools enable the smooth adaptation of commercial 3D printing processes, minimizing risks and improving print accuracy in the unique conditions of space.
To ensure high reliability and meet the stringent requirements of the space industry, our solution aligns with established standards such as NASA’s Software Engineering and Assurance Handbook (NASA-HDBK-2203) and the European Cooperation for Space Standardization guidelines (ECSS-E-ST-10C and ECSS-E-ST-40C). Our software integrates adaptive logic to monitor and respond to both space and machine conditions, using a structured approach (e.g., If {Space Condition} and {Machine Condition} Then {Implement Code}). This standards-based approach, supported by thorough checklists, enhances software resilience, ensuring each print operation is safe, effective, and compliant.
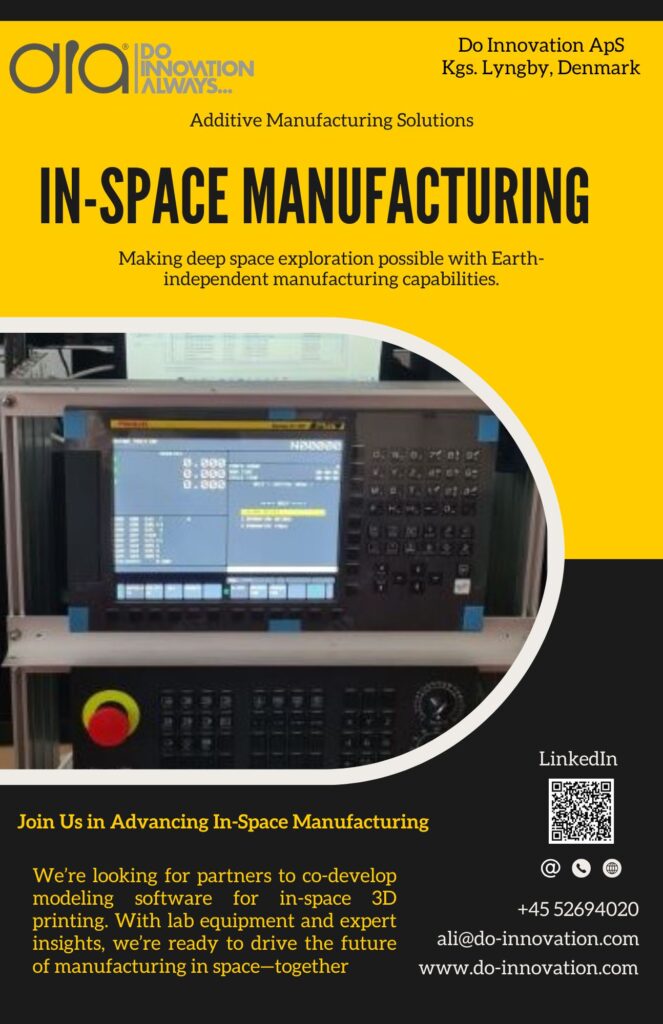